Lean: 104 años en movimiento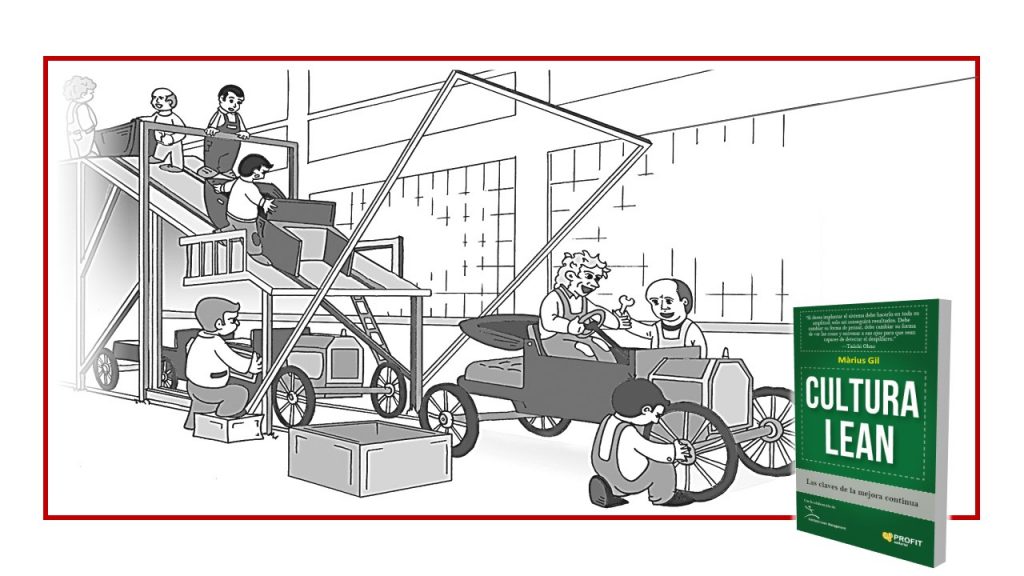
El 7 de octubre se celebra la puesta en marcha de la primera línea de producción en movimiento, posiblemente la principal contribución de Ford a la industria del automóvil y uno de los saltos tecnológicos más relevantes del sector.
No confundamos la línea en movimiento con el trabajo en línea que es anterior a esta época. Probablemente, deberíamos remontarnos hasta el siglo XIV para encontrar una primera aproximación a una línea de producción en el Arsenal de Venecia, unos fantásticos astilleros instalados en un único edificio pensado para construir grandes embarcaciones empleando un sistema que puede recordarnos las líneas de ensamblaje.
En cuanto al sector del automóvil debemos atribuir el mérito de diseñar y construir la primera línea de ensamblaje a Ransom E. Olds que en 1901 ya estaba construyendo los vehículos Oldsmobile con este sistema.
Primeros pasos ‘Lean’: Highland Park
La gran aportación del equipo de Henry Ford, liderado por Charles E. Sorensen fue la construcción de la primera línea de ensamblaje que funcionaba en movimiento continuo en la fábrica de Highland Park. El gran objetivo que perseguían era que las piezas llegaran a los operarios en lugar de ser ellos los que debieran desplazarse a buscarlas.
El año 1913 y después de varios años experimentando con los conceptos de creación de flujo en procesos productivos, los ingenieros de Ford consiguieron integrar toda la producción del modelo ‘T’ en un único edificio de seis plantas en el que cada sección trabajaba de forma cuasi-autónoma, entregando módulos y componentes a la línea principal de ensamblaje constituida por 82 estaciones y alimentada mediante cintas transportadoras a través de los miles de agujeros por los que se comunicaban las distintas secciones del edificio.
Resultados
A lo largo de más de una década Ford fue aumentado ininterrumpidamente la productividad y los volúmenes de producción de la planta de forma espectacular. Sirvan de ejemplo la evolución de los siguientes indicadores registrados por la propia compañía:
- Reducción del lead time de 21 a 14 días.
- Reducción del tiempo de producción de 750 a 93 minutos.
- Reducción del precio de venta del modelo ‘T’ de 700USD a 350USD en 5 años.
Estas líneas representan un modesto homenaje a uno de los principales monumentos industriales del siglo pasado, el edificio de Highland Park, que a pesar de tratarse de uno de los iconos de la segunda revolución industrial, actualmente se encuentra en un lamentable estado de degradación.
En el libro ‘cultura lean’ explicamos las contribuciones del sistema de producción de Ford a la cultura ‘lean’ y como evolucionó años después en Toyota hasta llegar a la actualidad.